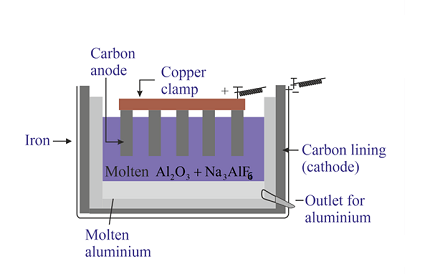
Aluminium is a highly reactive metal, which means that it readily reacts with oxygen in the air to form a protective layer of aluminium oxide. This layer helps to prevent further oxidation of the metal and makes it an attractive material for a wide range of applications.
The principles of metallurgy involve extracting metals from their ores and then refining them into a useful form. In the case of aluminium, the primary ore used is bauxite. Bauxite is a clay-like mineral that contains alumina, which is the primary source of aluminium.
The electrochemical principles of metallurgy involve using electricity to extract the metal from its ore. This process is known as electrolysis. In the case of aluminium, the ore is dissolved in molten cryolite (Na3AlF6) and then subjected to an electric current.
During electrolysis, the electric current causes the aluminium ions to move towards the cathode (negative electrode), while the oxygen ions move towards the anode (positive electrode). At the cathode, the aluminium ions are reduced to form aluminium metal, while at the anode, the oxygen ions are oxidized to form oxygen gas.
The process of electrolysis is highly energy-intensive, and as a result, aluminium production is a significant consumer of electricity. To reduce energy consumption, modern aluminium production facilities use advanced electrolytic cells and recycling processes to recover and reuse the energy required for the electrolysis process.
In addition to electrolysis, other principles of metallurgy are used in the production of aluminium. These include refining the metal to remove impurities and casting or shaping it into useful forms. Overall, the electrochemical principles of metallurgy play a critical role in the production of aluminium and other metals, enabling the extraction and refining of valuable materials that are essential for modern society.
What is Required Isolation of Metals Electrochemical (aluminium) principles of metallurgy
The isolation of metals using electrochemical principles of metallurgy requires the following steps:
- Mining and Extraction of Ore: The first step in isolating aluminium is the mining and extraction of bauxite ore. Bauxite is a clay-like mineral that contains alumina, which is the primary source of aluminium.
- Refining of Bauxite: Bauxite ore is refined to obtain alumina through the Bayer process. The Bayer process involves crushing and grinding the bauxite to a fine powder and then dissolving it in sodium hydroxide solution to form a sodium aluminate solution.
- Preparation of Cryolite: Cryolite is prepared by reacting sodium fluoride and aluminium fluoride in the presence of alumina. Cryolite is used as a solvent for alumina in the electrolysis process.
- Electrolysis: In the electrolysis process, the alumina is dissolved in molten cryolite and subjected to an electric current. The electric current causes the aluminium ions to move towards the cathode (negative electrode), while the oxygen ions move towards the anode (positive electrode). At the cathode, the aluminium ions are reduced to form aluminium metal, while at the anode, the oxygen ions are oxidized to form oxygen gas.
- Collection and Refining of Aluminium: The aluminium is collected at the cathode and then refined to remove impurities. The refining process involves melting the aluminium and then passing it through a series of filters and separators to remove any remaining impurities.
- Recycling: To reduce energy consumption, modern aluminium production facilities use advanced electrolytic cells and recycling processes to recover and reuse the energy required for the electrolysis process. Aluminium can be recycled infinitely, making it a sustainable and eco-friendly material.
Overall, the electrochemical principles of metallurgy play a critical role in the isolation of metals, including aluminium, and enable the extraction and refining of valuable materials that are essential for modern society.
When is Required Isolation of Metals Electrochemical (aluminium) principles of metallurgy
The electrochemical principles of metallurgy are used for the required isolation of metals when they are not found in their pure form in nature and need to be extracted from their ores. Metals such as aluminium, copper, zinc, and lead are extracted using the electrochemical principles of metallurgy.
The isolation of metals using electrochemical principles involves the use of electricity to separate the metal from its ore. This process is known as electrolysis and is a highly energy-intensive process. However, it is necessary to isolate these metals as they are essential for a wide range of modern applications, including construction, transportation, electronics, and more.
Aluminium, for example, is extracted from bauxite ore using the electrochemical principles of metallurgy. Bauxite ore is first refined to obtain alumina, which is then dissolved in molten cryolite and subjected to an electric current to isolate aluminium metal. This process is highly energy-intensive, but aluminium is a valuable material used extensively in various industries due to its lightweight, high strength, and excellent corrosion resistance.
Overall, the electrochemical principles of metallurgy are used for the required isolation of metals when they are not found in their pure form in nature and are essential for various applications in modern society.
Where is Required Isolation of Metals Electrochemical (aluminium) principles of metallurgy
The required isolation of metals using the electrochemical principles of metallurgy takes place in metallurgical industries, specifically in aluminum smelting plants. These plants use large-scale electrolysis to extract aluminum from its ore bauxite.
The largest producers of aluminum include China, Russia, Canada, the United Arab Emirates, and Australia. These countries have significant bauxite deposits and are home to large-scale aluminum smelting plants.
Aluminum smelting plants are typically located near sources of cheap electricity, such as hydroelectric power plants. This is because the electrolysis process used to extract aluminum is highly energy-intensive and requires a constant supply of electricity.
In addition to aluminum, other metals such as copper, zinc, and lead are also extracted using the electrochemical principles of metallurgy. The locations of these industries are typically based on the availability of the respective ores and sources of cheap electricity.
Overall, the required isolation of metals using the electrochemical principles of metallurgy takes place in metallurgical industries located in countries with significant deposits of the respective ores and sources of cheap electricity.
How is Required Isolation of Metals Electrochemical (aluminium) principles of metallurgy
The required isolation of metals using the electrochemical principles of metallurgy involves the following steps for the extraction of aluminium:
- Mining and Extraction of Ore: The first step is to mine bauxite ore, which is the primary source of aluminium. Bauxite is usually found close to the surface of the earth and can be extracted using open-pit mining.
- Refining of Bauxite: The mined bauxite ore is refined using the Bayer process to obtain alumina, which is the primary raw material used for the extraction of aluminium. In this process, the bauxite is crushed and mixed with sodium hydroxide solution to dissolve the alumina. The resulting solution is then purified and solidified to obtain alumina.
- Preparation of Cryolite: Cryolite is prepared by mixing aluminium fluoride, sodium fluoride, and fluorspar. Cryolite is used as a solvent to dissolve alumina in the electrolytic cell.
- Electrolysis: In the electrolytic cell, alumina is dissolved in molten cryolite and subjected to an electric current. The electric current causes the aluminium ions to move towards the cathode, while the oxygen ions move towards the anode. At the cathode, aluminium ions are reduced to form liquid aluminium, which is collected in the bottom of the cell. Oxygen ions combine to form oxygen gas at the anode.
- Collection and Refining of Aluminium: The liquid aluminium collected at the bottom of the cell is then further refined to remove any remaining impurities. The refining process involves passing the liquid aluminium through a series of filters and separators to remove any remaining impurities.
- Casting: The final step involves casting the refined aluminium into ingots or other forms as required for its intended use.
Overall, the required isolation of metals using the electrochemical principles of metallurgy involves a highly energy-intensive process that requires significant amounts of electricity. However, this process is essential for the extraction of metals such as aluminium that are widely used in various industries due to their desirable properties such as strength, light weight, and corrosion resistance.
Production of Isolation of Metals Electrochemical (aluminium) principles of metallurgy
The production of aluminium using the electrochemical principles of metallurgy involves several stages. Here are the main steps involved in the production of aluminium:
- Mining and Extraction of Bauxite: The first step is to mine bauxite, which is the primary source of aluminium. Bauxite is usually found close to the surface of the earth and can be extracted using open-pit mining.
- Refining of Bauxite: The mined bauxite ore is refined using the Bayer process to obtain alumina, which is the primary raw material used for the extraction of aluminium. In this process, the bauxite is crushed and mixed with sodium hydroxide solution to dissolve the alumina. The resulting solution is then purified and solidified to obtain alumina.
- Preparation of Cryolite: Cryolite is prepared by mixing aluminium fluoride, sodium fluoride, and fluorspar. Cryolite is used as a solvent to dissolve alumina in the electrolytic cell.
- Electrolysis: In the electrolytic cell, alumina is dissolved in molten cryolite and subjected to an electric current. The electric current causes the aluminium ions to move towards the cathode, while the oxygen ions move towards the anode. At the cathode, aluminium ions are reduced to form liquid aluminium, which is collected in the bottom of the cell. Oxygen ions combine to form oxygen gas at the anode.
- Collection and Refining of Aluminium: The liquid aluminium collected at the bottom of the cell is then further refined to remove any remaining impurities. The refining process involves passing the liquid aluminium through a series of filters and separators to remove any remaining impurities.
- Casting: The final step involves casting the refined aluminium into ingots or other forms as required for its intended use.
The production of aluminium using the electrochemical principles of metallurgy is a highly energy-intensive process that requires a constant supply of electricity. Therefore, aluminium smelters are typically located near sources of cheap electricity, such as hydroelectric power plants. The use of renewable sources of energy such as solar and wind power is also being explored to reduce the environmental impact of aluminium production.
Overall, the production of aluminium using the electrochemical principles of metallurgy involves several stages that require significant amounts of energy and careful attention to detail to produce high-quality aluminium suitable for various applications in modern society.
Case Study on Isolation of Metals Electrochemical (aluminium) principles of metallurgy
One example of the isolation of metals using the electrochemical principles of metallurgy is the production of aluminium by Rio Tinto, a mining and metals company.
Rio Tinto produces aluminium using the Hall-Héroult process, which is a variant of the Bayer process. The company mines bauxite in several locations around the world, including Australia, Guinea, and Canada. Once the bauxite is mined, it is transported to refineries where it is refined into alumina.
At Rio Tinto’s smelters, alumina is mixed with cryolite and other chemicals to create a molten electrolyte. The electrolyte is then heated to a temperature of around 960°C, and an electric current is passed through it. The electric current causes aluminium ions to move towards the cathode, where they are reduced to form liquid aluminium. Oxygen ions move towards the anode, where they combine to form oxygen gas.
Rio Tinto’s smelters are some of the most energy-efficient in the world, with an energy intensity of around 12.6 megajoules per kilogram of aluminium produced. The company has also set a target of reaching net-zero greenhouse gas emissions by 2050, and it is working on several initiatives to reduce its carbon footprint, including investing in renewable energy and developing new technologies for aluminium production.
Overall, Rio Tinto’s production of aluminium using the electrochemical principles of metallurgy is an example of how mining and metals companies can use innovative technologies to reduce their environmental impact while meeting the growing demand for metals in modern society. By continuously improving their processes and investing in sustainable practices, companies like Rio Tinto can contribute to a more sustainable future for the mining and metals industry.
White paper on Isolation of Metals Electrochemical (aluminium) principles of metallurgy
Introduction
The isolation of metals using the electrochemical principles of metallurgy has revolutionized the way we produce metals. Aluminium, one of the most widely used metals in modern society, is produced using this method. In this white paper, we will discuss the electrochemical principles of metallurgy and how they are applied in the production of aluminium.
Electrochemical Principles of Metallurgy
Electrochemistry is the study of the interaction between electricity and chemical reactions. Metallurgy, on the other hand, is the science of extracting metals from their ores, refining them, and preparing them for use. Electrochemical principles of metallurgy combine these two fields to isolate metals from their ores using electric currents.
The process involves subjecting a molten electrolyte to an electric current. The electrolyte contains metal ions and other elements that are attracted to the electrodes. The metal ions are reduced at the cathode to form the metal, while the other elements are oxidized at the anode. The metal is then collected at the bottom of the cell and further refined to remove any impurities.
Isolation of Aluminium using Electrochemical Principles of Metallurgy
The isolation of aluminium using electrochemical principles of metallurgy involves several stages. The first stage is mining and extracting bauxite, which is the primary source of aluminium. Bauxite is usually found close to the surface of the earth and can be extracted using open-pit mining.
The next stage is refining the bauxite using the Bayer process to obtain alumina. The bauxite is crushed and mixed with sodium hydroxide solution to dissolve the alumina. The resulting solution is then purified and solidified to obtain alumina.
The next stage involves preparing cryolite by mixing aluminium fluoride, sodium fluoride, and fluorspar. Cryolite is used as a solvent to dissolve alumina in the electrolytic cell.
In the electrolytic cell, alumina is dissolved in molten cryolite and subjected to an electric current. The electric current causes the aluminium ions to move towards the cathode, while the oxygen ions move towards the anode. At the cathode, aluminium ions are reduced to form liquid aluminium, which is collected in the bottom of the cell. Oxygen ions combine to form oxygen gas at the anode.
The liquid aluminium collected at the bottom of the cell is then further refined to remove any remaining impurities. The refining process involves passing the liquid aluminium through a series of filters and separators to remove any remaining impurities.
Conclusion
The isolation of metals using the electrochemical principles of metallurgy is an innovative and energy-intensive process that has revolutionized the way we produce metals. Aluminium, one of the most widely used metals in modern society, is produced using this method. The process involves several stages, including mining and extracting bauxite, refining it to obtain alumina, preparing cryolite, and subjecting the molten electrolyte to an electric current. The process requires a constant supply of electricity and careful attention to detail to produce high-quality aluminium suitable for various applications in modern society.