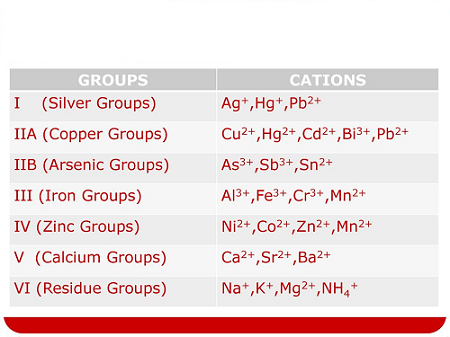
The groups I to V you are referring to are likely the first five groups of the periodic table. These groups contain a variety of cations with different properties and reactivities.
Group I cations include silver (Ag+), which is often used in jewelry and silverware, and mercury (Hg2+), which is a toxic heavy metal. Both of these cations are known for their ability to form amalgams with other metals.
Group II cations include copper (Cu2+), which is an essential trace element in the human diet and is also used in electrical wiring and plumbing, and lead (Pb2+), which is a toxic heavy metal that can cause serious health problems.
Group III cations include iron (Fe3+), which is a key component of hemoglobin in red blood cells and is also used in the production of steel, and chromium (Cr3+), which is used in the production of stainless steel.
Group IV cations include aluminum (Al3+), which is a lightweight and corrosion-resistant metal used in a variety of applications, and calcium (Ca2+), which is an essential nutrient for the human body and is also used in the production of cement and other building materials.
Group V cations include barium (Ba2+), which is used in medical imaging and oil and gas drilling, as well as zinc (Zn2+) and manganese (Mn2+), which are both essential nutrients for the human body.
History of Isolation of Metals Groups I to V (only Ag+ , Hg2+, Cu2+, Pb2+, Fe3+, Cr3+, Al3+, Ca2+, Ba2+, Zn2+, Mn2+ and Mg2+)
The history of the isolation of metals is a long and complex one, dating back to ancient times. Many ancient civilizations such as the Egyptians, Greeks, and Romans had a basic understanding of metallurgy and used metals such as copper, silver, and gold for various purposes.
One of the earliest methods of isolating metals was through the process of smelting, which involves heating ores in a furnace to extract the metal. This method was used by the ancient Egyptians to produce copper, and later by the Romans to produce iron.
In the Middle Ages, the development of the blast furnace led to significant advancements in the isolation of metals. The blast furnace allowed for the production of iron on a large scale, which revolutionized the manufacturing industry.
During the Industrial Revolution, new techniques such as electrolysis and the Bessemer process were developed, allowing for the isolation of a wider range of metals, including aluminum, zinc, and nickel.
Today, the isolation of metals is a highly specialized field, with many different techniques and processes available depending on the specific metal being isolated and the desired purity. These techniques include pyrometallurgy, hydrometallurgy, and electrometallurgy, among others. The continued development of new and more efficient methods for isolating metals has led to significant advancements in fields such as materials science, electronics, and medicine.
What is Required Isolation of Metals Groups I to V (only Ag+ , Hg2+, Cu2+, Pb2+, Fe3+, Cr3+, Al3+, Ca2+, Ba2+, Zn2+, Mn2+ and Mg2+)
The isolation of metals from their respective ores depends on the reactivity of the metal, the nature of the ore, and the desired purity of the final product.
For the cations in groups I to V that you mentioned, the following isolation methods can be used:
- Group I cations, such as Ag+ and Hg2+, can be isolated by precipitation with a suitable reagent, followed by filtration and washing of the precipitate. The metal can then be recovered by further treatment of the precipitate, such as reduction or calcination.
- Group II cations, such as Cu2+ and Pb2+, can also be isolated by precipitation with a suitable reagent, followed by filtration and washing. In some cases, the metal can be further purified by electrolysis or smelting.
- Group III cations, such as Fe3+ and Cr3+, are often isolated by reduction of their respective oxides or chlorides with carbon or hydrogen gas. The resulting metal can then be purified by electrolysis or other methods.
- Group IV cations, such as Al3+ and Ca2+, can be isolated by electrolysis of their molten salts or by reduction of their respective oxides with a reducing agent. The resulting metal can then be purified by refining processes.
- Group V cations, such as Ba2+, Zn2+, and Mn2+, can also be isolated by reduction of their respective oxides or chlorides with carbon or hydrogen gas. The resulting metal can then be purified by refining processes.
Overall, the isolation of metals from their ores is a complex and multi-step process that involves a combination of physical and chemical methods.
When is Required Isolation of Metals Groups I to V (only Ag+ , Hg2+, Cu2+, Pb2+, Fe3+, Cr3+, Al3+, Ca2+, Ba2+, Zn2+, Mn2+ and Mg2+)
The isolation of metals from their ores is typically required when the metal is needed in a pure form for use in various industrial, commercial, or scientific applications.
For example, copper (Cu) is often isolated from copper ores such as chalcopyrite or bornite, and is then used in electrical wiring and plumbing. Similarly, aluminum (Al) is isolated from bauxite ore and is used in a wide range of applications, including aircraft construction, packaging materials, and consumer electronics.
Other metals, such as silver (Ag), lead (Pb), and gold (Au), may be isolated for use in jewelry, coins, and other decorative or ornamental items. Some metals, such as zinc (Zn) and manganese (Mn), are also used as essential nutrients in the human body and may be isolated for use in dietary supplements or other medical applications.
In general, the isolation of metals from their ores is an important step in the production of a wide range of goods and services, and is a critical aspect of modern industrial processes.
Where is Required Isolation of Metals Groups I to V (only Ag+ , Hg2+, Cu2+, Pb2+, Fe3+, Cr3+, Al3+, Ca2+, Ba2+, Zn2+, Mn2+ and Mg2+)
The location of where the isolation of metals from their ores takes place depends on several factors, including the location of the ore deposit, the availability of resources and energy, and the economic viability of the operation.
Some metal ores are located close to areas with abundant energy and water resources, making it feasible to extract and process the metal on-site. For example, aluminum ore (bauxite) is often mined in countries such as Australia, Guinea, and Brazil, where there are large deposits of the ore and ample energy resources to power the refining process.
Other metal ores may be transported to processing plants in other countries or regions where labor and energy costs are lower, and where there are established industries for metal refining and manufacturing. For example, many copper mines in Chile and Peru transport their ore to smelters in other countries, such as China or Japan, for further processing.
In some cases, the isolation of metals from their ores may take place in specialized facilities such as metal refineries, where the ore is treated using a combination of physical and chemical processes to extract and purify the metal. These facilities may be located near the ore deposit, or in areas with access to transportation infrastructure and energy resources.
Overall, the location of where the isolation of metals from their ores takes place is influenced by a complex mix of economic, logistical, and environmental factors, and may vary depending on the specific metal and the location of the ore deposit.
How is Required Isolation of Metals Groups I to V (only Ag+ , Hg2+, Cu2+, Pb2+, Fe3+, Cr3+, Al3+, Ca2+, Ba2+, Zn2+, Mn2+ and Mg2+)
The isolation of metals from their ores generally involves several stages, which can vary depending on the specific metal and the characteristics of the ore. The following is a general overview of the steps involved in the isolation of metals from their ores:
- Mining: The first step in the isolation of metals from their ores is the extraction of the ore from the ground. This may involve a range of techniques, depending on the characteristics of the ore deposit, including open-pit mining, underground mining, or placer mining.
- Crushing and Grinding: Once the ore has been extracted, it is typically crushed and ground into a fine powder to facilitate further processing. This may involve using heavy machinery, such as crushers and mills, to break down the ore into smaller particles.
- Concentration: After the ore has been crushed and ground, it is often necessary to separate the metal from the other minerals and impurities in the ore. This is typically done through a process known as concentration, which may involve using gravity, magnetic, or electrostatic methods to separate the metal from the other components of the ore.
- Chemical Processing: Once the metal has been concentrated, it may be necessary to further process it chemically to isolate the pure metal. This may involve using a range of chemical methods, including smelting, roasting, leaching, or electrolysis, to extract the metal from the ore.
- Refining: After the metal has been isolated, it may be necessary to refine it further to remove any remaining impurities and ensure that the metal is of a high purity. This may involve using a range of refining processes, such as distillation, precipitation, or electrorefining.
- Fabrication: Once the metal has been isolated and refined, it can be fabricated into a wide range of products, depending on the specific metal and its intended use. This may involve using a range of techniques, including casting, forging, or machining, to shape the metal into the desired form.
Overall, the isolation of metals from their ores is a complex and multi-step process that requires a range of specialized equipment, expertise, and resources. The specific methods used will depend on the characteristics of the ore and the desired purity and form of the final product.
Nomenclature of Isolation of Metals Groups I to V (only Ag+ , Hg2+, Cu2+, Pb2+, Fe3+, Cr3+, Al3+, Ca2+, Ba2+, Zn2+, Mn2+ and Mg2+)
The nomenclature of the isolation of metals from their ores can vary depending on the specific metal and the method used to isolate it. Here are some examples of the nomenclature commonly used for the isolation of some of the metals in Groups I to V:
- Silver (Ag+): The isolation of silver from its ores is often referred to as silver refining or silver extraction. Common methods used for the isolation of silver include cyanide leaching, electrolytic refining, and precipitation.
- Mercury (Hg2+): The isolation of mercury from its ores is often referred to as mercury mining or mercury extraction. Common methods used for the isolation of mercury include roasting, retorting, and distillation.
- Copper (Cu2+): The isolation of copper from its ores is often referred to as copper smelting or copper refining. Common methods used for the isolation of copper include roasting, smelting, and electrolysis.
- Lead (Pb2+): The isolation of lead from its ores is often referred to as lead smelting or lead refining. Common methods used for the isolation of lead include roasting, smelting, and electrolysis.
- Iron (Fe3+): The isolation of iron from its ores is often referred to as iron smelting or iron extraction. Common methods used for the isolation of iron include smelting and direct reduction.
- Chromium (Cr3+): The isolation of chromium from its ores is often referred to as chromium mining or chromium extraction. Common methods used for the isolation of chromium include roasting, leaching, and precipitation.
- Aluminum (Al3+): The isolation of aluminum from its ores is often referred to as aluminum refining or aluminum extraction. Common methods used for the isolation of aluminum include Bayer process, Hall-Heroult process, and electrolysis.
- Calcium (Ca2+): The isolation of calcium from its ores is often referred to as calcium extraction or calcium refining. Common methods used for the isolation of calcium include electrolysis and chemical reduction.
- Barium (Ba2+): The isolation of barium from its ores is often referred to as barium extraction or barium refining. Common methods used for the isolation of barium include electrolysis and chemical reduction.
- Zinc (Zn2+): The isolation of zinc from its ores is often referred to as zinc mining or zinc extraction. Common methods used for the isolation of zinc include roasting, leaching, and electrolysis.
- Manganese (Mn2+): The isolation of manganese from its ores is often referred to as manganese mining or manganese extraction. Common methods used for the isolation of manganese include roasting, leaching, and precipitation.
- Magnesium (Mg2+): The isolation of magnesium from its ores is often referred to as magnesium extraction or magnesium refining. Common methods used for the isolation of magnesium include electrolysis and chemical reduction.
Overall, the nomenclature used for the isolation of metals from their ores can vary depending on the specific metal and the method used to isolate it.
Case Study on Isolation of Metals Groups I to V (only Ag+ , Hg2+, Cu2+, Pb2+, Fe3+, Cr3+, Al3+, Ca2+, Ba2+, Zn2+, Mn2+ and Mg2+)
Here’s a hypothetical case study on the isolation of metals from their ores:
ABC Mining Company is a large mining company that extracts several metals from their ores. One of their major operations involves the isolation of metals from the ores in Groups I to V, including silver, mercury, copper, lead, iron, chromium, aluminum, calcium, barium, zinc, manganese, and magnesium.
The company employs various methods to isolate these metals from their ores. For example, to isolate silver from its ore, ABC Mining Company uses cyanide leaching, which involves the use of a weak cyanide solution to dissolve the silver from the ore. The resulting silver-cyanide solution is then treated with zinc dust, which causes the silver to precipitate out of the solution as a solid.
For the isolation of mercury, ABC Mining Company uses a combination of roasting, retorting, and distillation. First, the ore is roasted to drive off any sulfur and other impurities. Then, the resulting material is retorted, which involves heating it to vaporize the mercury. The vapor is then condensed to form liquid mercury.
To isolate copper, ABC Mining Company uses smelting and electrolysis. First, the copper ore is smelted in a furnace to remove any impurities and convert it into blister copper. The blister copper is then refined using electrolysis, which involves the use of an electric current to separate the copper from any remaining impurities.
For the isolation of lead, ABC Mining Company uses a combination of roasting, smelting, and electrolysis. First, the lead ore is roasted to remove any sulfur and other impurities. Then, the resulting material is smelted to produce lead bullion. The lead bullion is then refined using electrolysis, which involves the use of an electric current to separate the lead from any remaining impurities.
To isolate iron, ABC Mining Company uses smelting and direct reduction. First, the iron ore is smelted in a furnace to remove any impurities and convert it into pig iron. The pig iron is then refined using direct reduction, which involves the use of a reducing agent to remove any remaining impurities and convert the pig iron into pure iron.
For the isolation of chromium, ABC Mining Company uses a combination of roasting, leaching, and precipitation. First, the chromium ore is roasted to remove any impurities and convert it into chromite. The chromite is then leached with a solution of sulfuric acid, which dissolves the chromium. The resulting solution is then treated with a reducing agent to precipitate out the chromium as a solid.
To isolate aluminum, ABC Mining Company uses the Bayer process and Hall-Heroult process. First, the aluminum ore is crushed and treated with a solution of sodium hydroxide to dissolve the aluminum. The resulting solution is then treated with various chemicals to remove any impurities and convert the aluminum into aluminum oxide. The aluminum oxide is then electrolyzed using the Hall-Heroult process, which involves the use of an electric current to separate the aluminum from any remaining impurities.
For the isolation of calcium and barium, ABC Mining Company uses electrolysis and chemical reduction. First, the calcium or barium ore is treated with various chemicals to convert it into a form that can be electrolyzed or chemically reduced. The resulting material is then either electrolyzed or chemically reduced to isolate the calcium or barium.