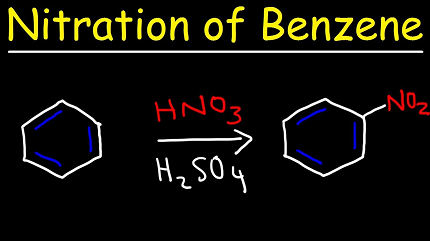
Benzene nitration is a chemical reaction in which a nitro group (-NO2) is introduced into the benzene molecule. This reaction is an important industrial process and is used to produce a variety of chemical compounds, such as explosives, dyes, and pharmaceuticals.
The nitration of benzene is typically carried out by treating benzene with a mixture of concentrated nitric acid and sulfuric acid. The reaction is highly exothermic and can be dangerous, so it must be carried out with caution and appropriate safety measures.
The overall reaction can be represented as follows:
C6H6 + HNO3 → C6H5NO2 + H2O
In this reaction, one of the hydrogen atoms in the benzene ring is replaced by a nitro group, resulting in the formation of nitrobenzene.
The reaction mechanism involves the formation of a highly reactive nitronium ion (NO2+) intermediate, which is generated by the reaction of nitric acid with sulfuric acid. The nitronium ion then attacks the benzene ring, resulting in the substitution of one of the hydrogen atoms with the nitro group.
Overall, benzene nitration is an important and widely used reaction in the chemical industry, and its mechanism has been extensively studied and understood.
What is Required Benzene Nitration
The reaction conditions required for benzene nitration are:
- Benzene: Benzene is the starting material for this reaction, and it is used in excess to drive the reaction forward.
- Nitric acid: Nitric acid is the source of the nitro group (-NO2) that is introduced into the benzene molecule. The concentration of nitric acid used is typically between 60-70% to ensure that enough nitronium ion is produced to react with benzene.
- Sulfuric acid: Sulfuric acid is used as a catalyst to generate the nitronium ion (NO2+), which is the electrophile that attacks the benzene ring.
- Temperature: The reaction is highly exothermic, meaning it produces heat as it progresses. Therefore, the reaction must be cooled to control the temperature and prevent a runaway reaction. The reaction is typically carried out between 0-10°C.
- Reaction vessel: The reaction must be carried out in a suitable reaction vessel made of materials that can withstand the corrosive nature of the acids used.
- Safety measures: The reaction is hazardous and must be carried out with appropriate safety measures, such as protective equipment, good ventilation, and careful handling of the chemicals involved.
Overall, benzene nitration requires careful control of the reaction conditions to ensure a successful and safe reaction.
When is Required Benzene Nitration
Benzene nitration is required in a variety of industrial processes where the introduction of a nitro group (-NO2) into a benzene ring is necessary. Some of the applications of benzene nitration include:
- Production of nitrobenzene: Nitrobenzene is an important industrial chemical used as a solvent and as a starting material for the production of other chemicals, such as aniline, which is used to make dyes and pharmaceuticals.
- Production of explosives: The nitro group in nitrobenzene can be further modified to produce explosive compounds such as trinitrotoluene (TNT) and picric acid.
- Production of pharmaceuticals: Nitrobenzene derivatives are used in the production of certain drugs, such as paracetamol and chloramphenicol.
- Production of dyes: Nitrobenzene derivatives are used in the production of certain dyes, such as azo dyes.
Overall, benzene nitration is an important reaction in the chemical industry and is used in a variety of applications where the introduction of a nitro group into a benzene ring is necessary.
Where is Required Benzene Nitration
Benzene nitration is carried out in chemical plants and laboratories where the production of various chemical compounds is required. The reaction is typically carried out in a suitable reaction vessel made of materials that can withstand the corrosive nature of the acids used.
Benzene nitration is a highly exothermic and hazardous reaction, so it must be carried out with appropriate safety measures, such as protective equipment, good ventilation, and careful handling of the chemicals involved. The reaction vessel must also be equipped with safety devices, such as pressure relief valves and emergency cooling systems, to prevent a runaway reaction.
The production of nitrobenzene, which is one of the main applications of benzene nitration, is typically carried out in large-scale chemical plants. The nitrobenzene is then used as a starting material for the production of other chemicals, such as aniline, which is used in the production of dyes and pharmaceuticals.
Overall, benzene nitration is an important reaction in the chemical industry and is carried out in various chemical plants and laboratories where the production of nitrobenzene and other chemical compounds is required.
How is Required Benzene Nitration
Benzene nitration is typically carried out using the following steps:
- Preparation of the reaction mixture: A mixture of concentrated nitric acid and sulfuric acid is prepared in a suitable container. The concentration of nitric acid used is typically between 60-70%, and sulfuric acid is used as a catalyst to generate the nitronium ion (NO2+), which is the electrophile that attacks the benzene ring.
- Cooling the reaction mixture: The reaction mixture is cooled to a temperature between 0-10°C to prevent a runaway reaction due to the highly exothermic nature of the reaction.
- Addition of benzene: Benzene is slowly added to the cooled reaction mixture while stirring. The addition of benzene should be slow and controlled to prevent the temperature from rising too quickly.
- Completion of the reaction: Once all the benzene has been added, the reaction mixture is stirred for a specific period, typically around 30 minutes. The completion of the reaction is usually monitored by TLC (thin-layer chromatography) or other analytical methods.
- Work-up: After the reaction is complete, the reaction mixture is quenched with water to stop the reaction. The mixture is then extracted with an organic solvent such as ether or dichloromethane to separate the product (nitrobenzene) from the reaction mixture.
- Purification: The product is purified by distillation or recrystallization to obtain pure nitrobenzene.
Overall, benzene nitration is a carefully controlled reaction that requires the use of appropriate safety measures and specialized equipment. The reaction is widely used in the chemical industry to produce a variety of chemical compounds such as explosives, dyes, and pharmaceuticals.
Nomenclature of Benzene Nitration
Benzene nitration results in the introduction of a nitro group (-NO2) into the benzene ring. The nomenclature of the resulting compound depends on the position of the nitro group on the benzene ring.
The positions on the benzene ring are numbered 1-6, starting from any arbitrary position and proceeding clockwise or counterclockwise around the ring. The position of the nitro group is indicated by the number of the carbon atom to which it is attached.
For example, if the nitro group is attached to the carbon atom in the first position, the resulting compound is called nitrobenzene. If the nitro group is attached to the carbon atom in the second position, the resulting compound is called o-nitrophenol. If the nitro group is attached to the carbon atom in the third position, the resulting compound is called m-nitrotoluene, and so on.
When multiple nitro groups are introduced into the benzene ring, the positions of the nitro groups are indicated by numbers separated by commas. For example, 1,3,5-trinitrobenzene has three nitro groups attached to the carbon atoms in the first, third, and fifth positions on the benzene ring.
In summary, the nomenclature of benzene nitration compounds follows the general rules of benzene derivatives, where the position of the nitro group is indicated by a number and the prefix (ortho-, meta-, or para-) is used when multiple substituents are present.
Case Study on Benzene Nitration
One example of the use of benzene nitration is in the production of nitrobenzene, which is an important starting material for the production of other chemicals, such as aniline, which is used in the production of dyes and pharmaceuticals.
In one case study, a chemical plant was producing nitrobenzene using a continuous process. The process involved the reaction of benzene with a mixture of nitric acid and sulfuric acid in a reactor vessel, followed by separation and purification of the nitrobenzene product.
The process was carefully monitored and controlled to ensure the safety of the workers and the quality of the product. Safety measures included the use of protective equipment, good ventilation, and emergency shutdown systems. The process was also designed to minimize waste and reduce the environmental impact of the production process.
The production process involved several key steps:
- Preparation of the reaction mixture: Nitric acid and sulfuric acid were mixed in the correct ratio and temperature to generate the nitronium ion, which is the electrophile that attacks the benzene ring.
- Addition of benzene: Benzene was continuously added to the reaction mixture while stirring, with the addition rate carefully controlled to prevent the temperature from rising too quickly.
- Reaction: The reaction mixture was allowed to react for a specific period, typically around 30 minutes. The reaction was carefully monitored to ensure that the reaction proceeded to completion and that no unreacted benzene remained.
- Separation and purification: The reaction mixture was quenched with water to stop the reaction, and the nitrobenzene product was extracted with an organic solvent. The product was then purified by distillation or recrystallization to obtain pure nitrobenzene.
Overall, the production of nitrobenzene using benzene nitration is an important process in the chemical industry, with many applications in the production of dyes, pharmaceuticals, and other chemicals. The process must be carefully controlled and monitored to ensure the safety of workers and the quality of the product.
White paper on Benzene Nitration
Introduction
Benzene nitration is a key process in the chemical industry, which involves the introduction of a nitro group (-NO2) into the benzene ring. Nitrobenzene, which is produced by benzene nitration, is an important starting material for the production of other chemicals, such as aniline, which is used in the production of dyes and pharmaceuticals. This white paper provides an overview of the benzene nitration process, including its chemistry, industrial applications, and safety considerations.
Chemistry of Benzene Nitration
Benzene nitration is a classic example of an electrophilic aromatic substitution reaction, which involves the attack of an electrophile on the aromatic ring. The electrophile in benzene nitration is the nitronium ion (NO2+), which is generated by the reaction of nitric acid and sulfuric acid:
HNO3 + H2SO4 -> NO2+ + HSO4- + H2O
The nitronium ion then attacks the benzene ring, leading to the formation of nitrobenzene:
C6H6 + NO2+ -> C6H5NO2 + H+
The reaction is typically carried out at elevated temperatures and with careful control of the reaction conditions to ensure that the reaction proceeds to completion and that no unwanted side reactions occur.
Industrial Applications of Benzene Nitration
Benzene nitration has numerous industrial applications, particularly in the production of aniline and other chemicals. Aniline is a key intermediate in the production of a wide range of dyes, pharmaceuticals, and other chemicals. Nitrobenzene is also used as a solvent, a chemical intermediate, and a starting material for the production of other chemicals.
In addition to its direct applications, benzene nitration is also used as a key step in the production of other chemicals, such as trinitrotoluene (TNT) and picric acid. TNT is a high explosive used in military applications, while picric acid is used as a yellow dye and in the production of explosives.
Safety Considerations in Benzene Nitration
Benzene nitration is a potentially hazardous process, and safety considerations are of paramount importance in its industrial application. One key concern is the generation of toxic byproducts, such as nitrous oxide (N2O) and sulfur dioxide (SO2), which can be harmful to both human health and the environment.
To minimize the risks associated with benzene nitration, a range of safety measures are employed. These include the use of protective equipment, such as goggles, gloves, and respirators, to protect workers from exposure to hazardous chemicals. Ventilation systems are also used to remove harmful gases from the work area and to prevent the buildup of explosive vapors.
Emergency response plans and procedures are also put in place to deal with accidents or unexpected events. These may include shutdown procedures, evacuation plans, and emergency response teams.
Conclusion
Benzene nitration is a key process in the chemical industry, with numerous applications in the production of dyes, pharmaceuticals, explosives, and other chemicals. The process involves the introduction of a nitro group into the benzene ring through an electrophilic aromatic substitution reaction, using the nitronium ion as the electrophile. Safety considerations are of paramount importance in the industrial application of benzene nitration, with a range of safety measures and emergency response procedures employed to minimize the risks associated with the process.