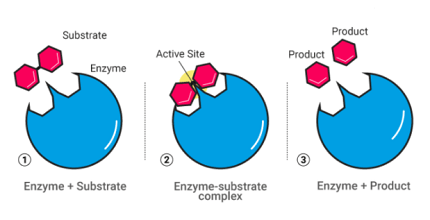
Solid catalysts are materials that accelerate chemical reactions by providing a surface for reactant molecules to adsorb onto and react. The activity of a solid catalyst is a measure of how effectively it can promote a particular chemical reaction, while selectivity refers to its ability to selectively form a desired product and minimize the formation of undesired byproducts.
Activity is influenced by factors such as the surface area, morphology, and composition of the catalyst. A catalyst with a higher surface area typically has more sites available for reactant molecules to adsorb onto, leading to increased activity. Morphology can also play a role, as catalysts with a more open or porous structure may provide better accessibility to reactants. The composition of the catalyst can also have a significant impact on activity, as different materials can have different electronic or acidic/basic properties that affect their ability to promote specific reactions.
Selectivity, on the other hand, is influenced by the specific chemical and structural properties of the catalyst. For example, a catalyst may have specific active sites that selectively promote the desired reaction pathway while minimizing the formation of undesired byproducts. The presence of specific metal or metal oxide components in a catalyst can also influence selectivity by providing specific sites for adsorption or reaction.
Overall, the activity and selectivity of solid catalysts are complex properties that depend on a range of factors, including the specific reaction being catalyzed, the structure and composition of the catalyst, and the reaction conditions. Careful selection and optimization of catalyst materials and operating conditions are necessary to achieve the desired activity and selectivity for a particular reaction.
What is Required Activity and selectivity of solid catalysts
The required activity and selectivity of a solid catalyst depend on the specific chemical reaction it is being used for and the desired product(s). In general, a catalyst must be sufficiently active to accelerate the reaction rate to a commercially viable level, while maintaining high selectivity for the desired product(s) to minimize the formation of unwanted byproducts.
The required activity of a catalyst will depend on factors such as the kinetics of the reaction, the desired reaction rate, and the process conditions. For example, if the reaction is slow or requires high temperatures, a highly active catalyst may be necessary to achieve a viable reaction rate. In contrast, if the reaction is fast, a less active catalyst may be sufficient.
The required selectivity of a catalyst will depend on the desired product(s) and the economic considerations of the process. For example, in the production of a specific chemical, the catalyst must be highly selective for the desired product to minimize the formation of byproducts, which can reduce yields and increase processing costs. However, in other cases, such as the use of catalysts in the purification of natural gas, a certain degree of selectivity may not be as critical.
In some cases, the activity and selectivity of a catalyst may be in conflict with each other, and a balance must be struck between these two properties. For example, a highly active catalyst may promote multiple reaction pathways, leading to lower selectivity, while a highly selective catalyst may have lower activity, leading to slower reaction rates. In these cases, careful catalyst design and optimization are necessary to achieve the desired balance between activity and selectivity.
When is Required Activity and selectivity of solid catalysts
The required activity and selectivity of solid catalysts are important considerations in a wide range of industrial chemical processes, as well as in research and development of new catalysts.
In the chemical industry, solid catalysts are used for a variety of applications, such as in the production of petrochemicals, plastics, pharmaceuticals, and food additives. In each of these applications, the required activity and selectivity of the catalyst will depend on the specific reaction being catalyzed and the desired products. For example, in the production of polyethylene, a highly active and selective catalyst is necessary to achieve high yields and minimize byproducts.
In addition to industrial applications, solid catalysts are also used in research and development to investigate new chemical reactions and develop new catalysts with improved properties. In these cases, the required activity and selectivity will depend on the specific research goals and the desired outcomes. For example, researchers may be interested in developing a highly active and selective catalyst for a specific reaction, or in studying the fundamental mechanisms of catalysis to gain insights into how to design more effective catalysts.
Overall, the required activity and selectivity of solid catalysts are critical considerations in both industrial and research applications, and careful catalyst design and optimization are necessary to achieve the desired outcomes.
Where is Required Activity and selectivity of solid catalysts
The required activity and selectivity of solid catalysts are important considerations in a wide range of chemical processes, including in the chemical industry, academic research, and environmental applications.
In the chemical industry, solid catalysts are used for various applications, such as in the production of polymers, fuels, and chemicals. The required activity and selectivity of the catalysts will depend on the specific reaction being catalyzed and the desired products. For example, in the production of high-density polyethylene, a highly active and selective catalyst is necessary to achieve high yields and minimize byproducts.
In academic research, solid catalysts are used to investigate new chemical reactions and develop new catalysts with improved properties. Researchers may be interested in developing highly active and selective catalysts for specific reactions or studying the fundamental mechanisms of catalysis to design more effective catalysts.
In environmental applications, solid catalysts can be used to remove pollutants from air and water. For example, catalysts can be used in the catalytic converters of automobiles to convert harmful emissions into less toxic gases. In these applications, the required activity and selectivity of the catalysts will depend on the specific pollutant being targeted and the desired removal efficiency.
Overall, the required activity and selectivity of solid catalysts are critical considerations in a wide range of applications, and careful catalyst design and optimization are necessary to achieve the desired outcomes.
How is Required Activity and selectivity of solid catalysts
The required activity and selectivity of solid catalysts can be influenced by various factors, including the catalyst material, structure, preparation method, and reaction conditions.
Catalyst material: The choice of catalyst material can have a significant impact on its activity and selectivity. Catalysts can be made from a wide range of materials, including metals, metal oxides, and zeolites, each with different properties and reactivities. The choice of catalyst material will depend on the specific reaction being catalyzed and the desired products.
Catalyst structure: The structure of the catalyst can also impact its activity and selectivity. Catalysts can be structured in different ways, such as nanoparticles, nanowires, and thin films, with different surface areas, surface chemistries, and catalytic properties. The structure of the catalyst can be tailored to enhance its activity and selectivity for specific reactions.
Preparation method: The preparation method of the catalyst can also impact its activity and selectivity. Different methods, such as impregnation, precipitation, and sol-gel, can lead to catalysts with different properties and catalytic activities. The choice of preparation method will depend on the desired catalyst properties and reaction conditions.
Reaction conditions: The reaction conditions, such as temperature, pressure, and reactant concentrations, can also impact the activity and selectivity of the catalyst. Different catalysts may have different optimal reaction conditions, and optimizing the reaction conditions can enhance the activity and selectivity of the catalyst.
In addition to these factors, careful catalyst design and optimization are necessary to achieve the desired balance between activity and selectivity. Catalysts can be modified and optimized by introducing dopants, changing the catalyst support, or modifying the catalyst surface to achieve the desired properties. Overall, a combination of careful catalyst design, preparation, and optimization is necessary to achieve the required activity and selectivity of solid catalysts.
Production of Activity and selectivity of solid catalysts
The production of solid catalysts with the desired activity and selectivity can be a complex process that involves various steps, including catalyst design, synthesis, characterization, and testing.
Catalyst design: The first step in the production of solid catalysts is to design the catalyst with the desired properties. This involves selecting the appropriate catalyst material, structure, and preparation method, based on the specific reaction being catalyzed and the desired products.
Catalyst synthesis: Once the catalyst design is complete, the next step is to synthesize the catalyst. This involves preparing the catalyst material using the chosen synthesis method, such as impregnation, precipitation, or sol-gel, and then shaping the material into the desired form, such as pellets, granules, or powders.
Catalyst characterization: After synthesis, the catalyst must be characterized to determine its physical and chemical properties. This involves using various analytical techniques, such as X-ray diffraction, scanning electron microscopy, and infrared spectroscopy, to examine the catalyst’s structure, surface area, surface chemistry, and other properties that may impact its activity and selectivity.
Catalyst testing: Finally, the synthesized and characterized catalyst must be tested for its activity and selectivity. This involves evaluating the catalyst’s performance in the specific reaction of interest, under varying reaction conditions, such as temperature, pressure, and reactant concentrations. The results of the testing can then be used to optimize the catalyst design and synthesis process, to improve the catalyst’s activity and selectivity.
Overall, the production of solid catalysts with the desired activity and selectivity involves a combination of careful catalyst design, synthesis, characterization, and testing, with the goal of optimizing the catalyst’s properties and performance for the specific reaction being catalyzed.
Case Study on Activity and selectivity of solid catalysts
One example of the importance of activity and selectivity of solid catalysts is in the production of propylene through the methanol-to-olefins (MTO) reaction. Propylene is an important building block for the production of polymers, and the MTO reaction provides an attractive alternative to the traditional petrochemical route for propylene production.
The MTO reaction involves the conversion of methanol to olefins, such as ethylene and propylene, over a solid catalyst. The activity and selectivity of the catalyst are critical for achieving high yields of the desired products, particularly propylene.
One study published in the journal ACS Catalysis in 2020 investigated the effect of catalyst acidity on the activity and selectivity of the MTO reaction. The researchers synthesized a series of SAPO-34 catalysts with varying acidity levels, and then tested their performance in the MTO reaction under different reaction conditions.
The results showed that the catalyst acidity had a significant impact on the activity and selectivity of the MTO reaction. Catalysts with higher acidity levels showed higher propylene selectivity, but lower methanol conversion, while catalysts with lower acidity levels showed higher methanol conversion, but lower propylene selectivity. The researchers also found that the optimal acidity level for propylene production was around 0.6-0.7 mmol/g.
The study highlights the importance of carefully optimizing the acidity of the catalyst in order to achieve the desired balance between activity and selectivity for the MTO reaction. By tuning the catalyst acidity, it may be possible to improve the propylene yield and selectivity in the MTO reaction, providing a more sustainable and efficient route for propylene production.
White paper on Activity and selectivity of solid catalysts
Here is a white paper on the topic of activity and selectivity of solid catalysts:
Introduction
Solid catalysts play a critical role in many chemical processes, including the production of fuels, chemicals, and materials. The activity and selectivity of these catalysts are key parameters that determine their performance and efficiency in catalyzing specific reactions.
Activity refers to the ability of a catalyst to promote a chemical reaction, typically measured by the rate of the reaction or the turnover frequency (TOF). Selectivity refers to the ability of a catalyst to produce the desired products of a reaction, while minimizing the formation of unwanted byproducts.
The activity and selectivity of solid catalysts depend on various factors, including the catalyst material, structure, composition, surface area, and surface chemistry, as well as the reaction conditions, such as temperature, pressure, and reactant concentrations.
In this white paper, we will discuss the importance of activity and selectivity of solid catalysts, and provide examples of how these parameters can be optimized for specific chemical processes.
Importance of Activity and Selectivity
The activity and selectivity of solid catalysts are critical for achieving high yields and efficiencies in many chemical processes. For example, in the production of fuels, such as gasoline and diesel, catalysts are used to convert crude oil into high-quality products with low sulfur and nitrogen content.
In the production of chemicals, such as polymers and pharmaceuticals, catalysts are used to control the reaction pathways and selectivity, enabling the production of specific products with desired properties.
In addition to improving the efficiency and sustainability of chemical processes, the optimization of catalyst activity and selectivity can also lead to cost savings and reduced waste, by minimizing the use of expensive or toxic reactants and reducing the formation of unwanted byproducts.
Optimization of Activity and Selectivity
The optimization of activity and selectivity of solid catalysts involves a combination of catalyst design, synthesis, characterization, and testing, as well as process optimization.
Catalyst Design:
The first step in optimizing catalyst activity and selectivity is to design the catalyst with the desired properties. This involves selecting the appropriate catalyst material, structure, and preparation method, based on the specific reaction being catalyzed and the desired products.
Catalyst Synthesis:
Once the catalyst design is complete, the next step is to synthesize the catalyst using the chosen synthesis method, such as impregnation, precipitation, or sol-gel, and then shaping the material into the desired form, such as pellets, granules, or powders.
Catalyst Characterization:
After synthesis, the catalyst must be characterized to determine its physical and chemical properties. This involves using various analytical techniques, such as X-ray diffraction, scanning electron microscopy, and infrared spectroscopy, to examine the catalyst’s structure, surface area, surface chemistry, and other properties that may impact its activity and selectivity.
Catalyst Testing:
Finally, the synthesized and characterized catalyst must be tested for its activity and selectivity. This involves evaluating the catalyst’s performance in the specific reaction of interest, under varying reaction conditions, such as temperature, pressure, and reactant concentrations. The results of the testing can then be used to optimize the catalyst design and synthesis process, to improve the catalyst’s activity and selectivity.
Process Optimization:
Once the optimal catalyst has been synthesized and characterized, the next step is to optimize the process conditions to maximize the catalyst’s performance. This may involve adjusting the reaction temperature, pressure, and reactant concentrations, as well as optimizing the catalyst loading, reaction time, and other parameters.
Conclusion:
In conclusion, the activity and selectivity of solid catalysts are important parameters that determine the efficiency and sustainability of many chemical processes. Optimizing the activity and selectivity of solid catalysts involves a multi-step process that includes catalyst design, synthesis, characterization, testing, and process optimization. The goal is to design and synthesize catalysts that exhibit high activity and selectivity, while minimizing waste and reducing the use of expensive or toxic reactants. By optimizing the activity and selectivity of solid catalysts, we can improve the efficiency and sustainability of chemical processes, leading to cost savings and environmental benefits.