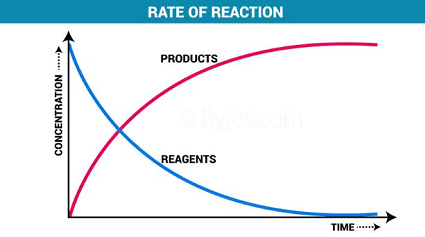
Chemical reactions can occur at different rates, depending on several factors such as temperature, concentration of reactants, the presence of a catalyst, surface area of reactants, and the nature of the reactants. The rate of a chemical reaction is defined as the change in concentration of reactants or products per unit time.
The rate of a chemical reaction can be expressed mathematically using the rate equation, which relates the rate of the reaction to the concentrations of the reactants. The rate equation is generally of the form:
rate = k[A]^m[B]^n
where [A] and [B] are the concentrations of reactants A and B, k is the rate constant, and m and n are the reaction orders with respect to A and B, respectively.
The rate constant is a proportionality constant that depends on the nature of the reaction and the temperature. The reaction orders m and n determine how the rate of the reaction changes with the concentrations of the reactants. For example, if the reaction order with respect to A is 2, doubling the concentration of A will quadruple the rate of the reaction.
The temperature also affects the rate of a chemical reaction. In general, an increase in temperature increases the rate of a reaction because it increases the kinetic energy of the reactant molecules, making them more likely to collide and react.
Catalysts are substances that increase the rate of a chemical reaction without being consumed in the reaction. They work by providing an alternative reaction pathway with a lower activation energy, making it easier for the reactant molecules to form products.
In summary, the rate of a chemical reaction is influenced by several factors, including temperature, concentration of reactants, the presence of a catalyst, surface area of reactants, and the nature of the reactants. These factors can be described mathematically using the rate equation, which relates the rate of the reaction to the concentrations of the reactants and the rate constant.
What is Required Rates of chemical reactions
Required rates of chemical reactions refer to the rates at which a reaction needs to occur in order to achieve a desired outcome, such as producing a certain amount of product in a given amount of time.
For example, in industrial processes, it is often necessary to produce a large amount of product in a short period of time. In this case, the reaction rate must be increased to meet the production requirements. This can be achieved by increasing the temperature, increasing the concentration of reactants, using a catalyst, or a combination of these factors.
In other cases, such as in biochemical reactions in the body, it is important to maintain a specific rate of reaction. Too slow of a reaction rate can lead to insufficient production of essential compounds, while too fast of a reaction rate can lead to the buildup of harmful byproducts. In these cases, the rate of reaction must be carefully controlled and regulated to maintain the desired outcome.
Overall, required rates of chemical reactions depend on the specific application and desired outcome, and can be achieved through a variety of factors that influence the rate of the reaction.
When is Required Rates of chemical reactions
The concept of required rates of chemical reactions is applicable in a variety of situations where chemical reactions are important. Some examples include:
- Industrial processes: In manufacturing, it is often necessary to produce a large amount of product in a short amount of time. This requires controlling the rate of chemical reactions to achieve the desired outcome.
- Biological processes: Many biochemical reactions in the body are regulated to occur at specific rates. For example, enzymes are used to speed up reactions that would otherwise occur too slowly to sustain life.
- Environmental processes: Chemical reactions occur in natural systems, such as the atmosphere, oceans, and soil. Understanding the rates at which these reactions occur is important for predicting and mitigating environmental impacts.
In general, the concept of required rates of chemical reactions is applicable whenever it is necessary to achieve a desired outcome through chemical processes, whether in industry, biology, or the environment.
Where is Required Rates of chemical reactions
The concept of required rates of chemical reactions is relevant in various fields and applications, including:
- Chemical industry: The chemical industry is a major user of chemical reactions, and requires precise control of reaction rates to maximize efficiency and productivity.
- Biotechnology: Biotechnology relies on chemical reactions, such as enzymatic reactions, to produce desired products or modify biological systems. The rate of these reactions needs to be controlled to achieve the desired outcome.
- Environmental science: Chemical reactions play a key role in many environmental processes, such as atmospheric chemistry and water treatment. Understanding the rates at which these reactions occur is important for predicting and mitigating environmental impacts.
- Materials science: Many materials are produced through chemical reactions, such as polymers and ceramics. The rate of these reactions affects the properties of the resulting materials.
Overall, the concept of required rates of chemical reactions is relevant in a wide range of fields and applications where chemical processes are involved.
How is Required Rates of chemical reactions
The required rates of chemical reactions can be achieved through various methods, which are dependent on the specific application and desired outcome. Some common methods for controlling the rate of chemical reactions include:
- Temperature control: Increasing the temperature generally increases the rate of a chemical reaction by increasing the kinetic energy of the reactant molecules and making them more likely to collide and react.
- Concentration control: Increasing the concentration of reactants generally increases the rate of a reaction by increasing the number of collisions between reactant molecules.
- Use of catalysts: Catalysts are substances that increase the rate of a chemical reaction without being consumed in the reaction. They work by providing an alternative reaction pathway with a lower activation energy, making it easier for the reactant molecules to form products.
- Surface area control: Increasing the surface area of reactants can increase the rate of reaction by exposing more reactant molecules to each other.
- Pressure control: In some reactions, increasing the pressure can increase the rate of reaction by forcing more reactant molecules closer together, increasing the frequency of collisions.
Overall, the methods used to achieve the required rates of chemical reactions depend on the specific application and desired outcome. By controlling factors such as temperature, concentration, use of catalysts, surface area, and pressure, it is possible to optimize the rate of chemical reactions to achieve the desired outcome.
Production of Rates of chemical reactions
The production of rates of chemical reactions refers to the process of increasing or optimizing the rate of a chemical reaction to achieve a desired outcome, such as producing a certain amount of product in a given amount of time. This is often a critical aspect of many industrial processes, where production efficiency and speed are key factors.
To increase the production of rates of chemical reactions, various techniques can be employed, such as:
- Optimization of reaction conditions: The reaction conditions, including temperature, pressure, concentration, and pH, can be optimized to increase the rate of the chemical reaction. For example, increasing the temperature can increase the rate of reaction, while lowering the pH can activate certain enzymes to catalyze a reaction.
- Use of catalysts: Catalysts can be used to increase the rate of a chemical reaction by lowering the activation energy required for the reaction to occur. This can reduce the time and energy needed for the reaction to proceed, leading to faster production rates.
- Mixing and agitation: Mixing and agitation can increase the rate of a chemical reaction by increasing the contact between reactants, allowing for more collisions and faster reactions.
- Continuous flow systems: Continuous flow systems can be used to optimize the production of rates of chemical reactions by allowing for a continuous flow of reactants, reducing reaction times and increasing productivity.
Overall, the production of rates of chemical reactions is a crucial aspect of many industrial processes. By optimizing reaction conditions, using catalysts, and employing mixing and agitation techniques, it is possible to increase production rates and achieve the desired outcome.
Case Study on Rates of chemical reactions
One example of a case study on rates of chemical reactions involves the production of ammonia through the Haber-Bosch process. The Haber-Bosch process is a key industrial process for the production of ammonia, which is used in the production of fertilizers and other industrial processes.
The Haber-Bosch process involves the reaction of nitrogen and hydrogen gases to produce ammonia:
N2 + 3H2 ⇌ 2NH3
This reaction is exothermic, meaning that it releases heat as it proceeds. However, the reaction is also relatively slow and requires high temperatures and pressures to proceed at a reasonable rate.
To optimize the rate of the Haber-Bosch reaction and increase production efficiency, various techniques are employed. These include:
- Catalysts: Iron catalysts are used to increase the rate of the reaction by lowering the activation energy required for the reaction to proceed.
- Temperature and pressure control: The temperature and pressure of the reaction can be controlled to optimize the rate of the reaction. Higher temperatures and pressures can increase the rate of the reaction, but can also lead to higher energy consumption and equipment costs.
- Recycling unreacted gases: The unreacted nitrogen and hydrogen gases are recycled back into the process to increase the yield of ammonia and improve production efficiency.
Through the optimization of reaction conditions and the use of catalysts, the Haber-Bosch process has been highly successful in producing ammonia at a large scale. However, there are also concerns about the environmental impact of the process, as it requires high energy consumption and produces greenhouse gas emissions. As a result, research is ongoing to develop more sustainable and efficient processes for ammonia production.
White paper on Rates of chemical reactions
White Paper: The Importance of Controlling Rates of Chemical Reactions
Introduction:
Rates of chemical reactions are a critical aspect of many industrial processes, as they directly impact the efficiency, cost, and quality of the end product. In this white paper, we will discuss the importance of controlling rates of chemical reactions and explore some of the methods used to achieve the required rates.
Importance of Controlling Rates of Chemical Reactions:
Controlling rates of chemical reactions is important for several reasons. Firstly, it can improve production efficiency by reducing the time and resources needed for a reaction to occur. This is particularly important in industrial processes where time is a critical factor and where large-scale production is required.
Secondly, controlling rates of chemical reactions can help to improve the quality and consistency of the end product. By optimizing the reaction conditions, it is possible to produce a product with a consistent quality and purity, which is important in many industries, such as pharmaceuticals and food production.
Finally, controlling rates of chemical reactions can also help to reduce costs by minimizing the amount of raw materials and energy needed to produce a certain amount of product. This is important for companies looking to increase profitability and reduce their environmental impact.
Methods for Controlling Rates of Chemical Reactions:
There are several methods for controlling rates of chemical reactions, which are dependent on the specific application and desired outcome. Some common methods include:
- Temperature control: Increasing or decreasing the temperature can directly impact the rate of a chemical reaction. Increasing the temperature increases the kinetic energy of the reactant molecules, making them more likely to collide and react, while decreasing the temperature slows down the reaction.
- Concentration control: Increasing the concentration of reactants can increase the rate of a reaction by increasing the number of collisions between reactant molecules.
- Use of catalysts: Catalysts are substances that increase the rate of a chemical reaction without being consumed in the reaction. They work by providing an alternative reaction pathway with a lower activation energy, making it easier for the reactant molecules to form products.
- Surface area control: Increasing the surface area of reactants can increase the rate of reaction by exposing more reactant molecules to each other.
- Pressure control: In some reactions, increasing the pressure can increase the rate of reaction by forcing more reactant molecules closer together, increasing the frequency of collisions.
Conclusion:
Controlling rates of chemical reactions is a crucial aspect of many industrial processes, as it directly impacts production efficiency, product quality, and cost. By optimizing reaction conditions and employing methods such as temperature control, concentration control, use of catalysts, surface area control, and pressure control, it is possible to achieve the required rates of chemical reactions and produce high-quality products in a more efficient and sustainable manner.