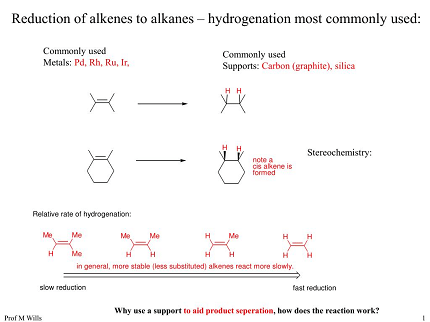
Reduction of alkenes and alkynes involves the addition of hydrogen atoms to the carbon-carbon double or triple bond, respectively. This process is known as hydrogenation and can be accomplished through several methods.
One common method is catalytic hydrogenation, which involves the use of a catalyst, such as platinum or palladium, to promote the reaction. The alkene or alkyne is typically dissolved in a solvent, such as an alcohol, and then mixed with the catalyst and hydrogen gas. The reaction proceeds under mild conditions, typically at room temperature and atmospheric pressure.
Another method is called dissolving metal reduction, which involves the use of an alkali metal, such as sodium or lithium, dissolved in a liquid ammonia solution. The alkene or alkyne is added to the solution, and the metal reduces the double or triple bond to a single bond.
Reduction of alkenes and alkynes is an important reaction in organic chemistry, as it can be used to synthesize a wide range of compounds, including alkanes, alcohols, and amines.
What is Required Reduction of Alkenes and Alkynes
The reduction of alkenes and alkynes typically requires a reducing agent, which is a chemical species that can donate electrons to the double or triple bond, thereby breaking it and forming a new single bond.
One common reducing agent used in the reduction of alkenes and alkynes is hydrogen gas (H2). This is usually employed in catalytic hydrogenation, where the reaction is carried out in the presence of a metal catalyst, such as palladium (Pd) or platinum (Pt).
Other reducing agents that can be used for the reduction of alkenes and alkynes include metal hydrides, such as sodium borohydride (NaBH4), lithium aluminum hydride (LiAlH4), and sodium metal (Na). These agents are usually employed in dissolving metal reduction or other reduction reactions.
The choice of reducing agent and reaction conditions depends on the specific reactants and desired products, as well as the desired reaction rate and selectivity. In some cases, multiple steps may be required to achieve the desired reduction.
When is Required Reduction of Alkenes and Alkynes
Reduction of alkenes and alkynes is commonly required in organic synthesis, where it can be used to convert unsaturated hydrocarbons into saturated hydrocarbons or to introduce new functional groups.
For example, reduction of an alkene can convert it into an alkane, which is a more stable and less reactive compound. This process is often used in the production of fuels and other industrial chemicals. Reduction of an alkyne can produce an alkene or an alkane, depending on the reaction conditions.
Reduction of alkenes and alkynes can also be used to introduce new functional groups, such as alcohols or amines. For example, reduction of an alkyne followed by reaction with ammonia can produce an unsaturated amine.
Overall, the reduction of alkenes and alkynes is a fundamental transformation in organic chemistry that is used in a wide range of applications, including the production of pharmaceuticals, polymers, and other industrial chemicals.
Where is Required Reduction of Alkenes and Alkynes
The reduction of alkenes and alkynes is a common reaction in organic chemistry and is used in a variety of fields and industries, including:
- Petrochemical industry: The reduction of alkenes is an important step in the production of gasoline, diesel, and other fuels from crude oil.
- Polymer industry: The reduction of alkynes can be used to prepare monomers that are used in the production of polymers such as polyethylene, polypropylene, and polyacetylene.
- Pharmaceutical industry: The reduction of alkenes and alkynes is used in the synthesis of many pharmaceuticals, such as statins and antibiotics.
- Food industry: Reduction of alkenes is used in the production of margarine, which is made from unsaturated vegetable oils that are partially hydrogenated to form saturated fats.
- Fine chemicals industry: Reduction of alkenes and alkynes is used to prepare a wide variety of specialty chemicals, including fragrances, flavors, and agrochemicals.
Overall, the reduction of alkenes and alkynes is a fundamental transformation in organic chemistry that is used in a wide range of applications in industry and academia.
How is Required Reduction of Alkenes and Alkynes
The reduction of alkenes and alkynes can be accomplished through several methods, depending on the specific reactants and desired products. Here are some of the most common methods:
- Catalytic hydrogenation: This method involves the use of a catalyst, such as palladium (Pd) or platinum (Pt), to promote the addition of hydrogen to the double or triple bond of the alkene or alkyne. The reaction is typically carried out in the presence of a solvent, such as ethanol, and under mild conditions of temperature and pressure.
- Dissolving metal reduction: This method involves the use of an alkali metal, such as sodium or lithium, dissolved in a liquid ammonia solution. The alkene or alkyne is added to the solution, and the metal reduces the double or triple bond to a single bond.
- Borane reduction: This method involves the use of borane (BH3) or borane derivatives, such as borane dimethyl sulfide (BH3-DMF), to add a hydride (H-) to the double or triple bond of the alkene or alkyne. The reaction is typically carried out in a solvent, such as tetrahydrofuran (THF), and under mild conditions of temperature and pressure.
- Sodium amalgam reduction: This method involves the use of sodium metal (Na) dissolved in a mercury (Hg) solution. The alkene or alkyne is added to the solution, and the sodium amalgam reduces the double or triple bond to a single bond.
Overall, the choice of method depends on the specific reactants and desired products, as well as the desired reaction rate and selectivity. Each method has its advantages and limitations, and it is important to select the appropriate method for a given reaction.
Production of Reduction of Alkenes and Alkynes
The production of reduction of alkenes and alkynes is typically carried out on an industrial scale using large-scale reactors and specialized equipment. Here are some common methods for the production of reduction of alkenes and alkynes:
- Catalytic hydrogenation: This method is used in the production of fuels and other chemicals from crude oil or natural gas. The feedstock, such as propylene or acetylene, is reacted with hydrogen gas in the presence of a metal catalyst, such as palladium or nickel, at high pressure and temperature.
- Sodium amalgam reduction: This method is used in the production of vinyl chloride, which is a key intermediate in the production of polyvinyl chloride (PVC). Ethylene gas is reacted with hydrogen chloride gas in the presence of a catalyst to produce vinyl chloride, which is then reduced with a sodium amalgam to produce ethylene dichloride.
- Borane reduction: This method is used in the production of pharmaceuticals and specialty chemicals. The alkene or alkyne is reacted with borane or a borane derivative in a solvent, such as THF, under mild conditions of temperature and pressure.
- Dissolving metal reduction: This method is used in the production of pharmaceuticals and agrochemicals. The alkene or alkyne is reacted with an alkali metal, such as sodium or lithium, dissolved in liquid ammonia under controlled conditions.
Overall, the production of reduction of alkenes and alkynes is a complex process that requires specialized equipment and expertise. The choice of method depends on the specific reactants and desired products, as well as the desired reaction rate and selectivity.
Case Study on Reduction of Alkenes and Alkynes
One example of the reduction of alkenes and alkynes is the production of margarine. Margarine is a spread made from vegetable oils that have been partially hydrogenated to produce a more solid consistency. This process involves the reduction of the unsaturated double bonds in the vegetable oils to saturated single bonds, which results in the formation of trans-fats.
The reduction of the double bonds in the vegetable oils is typically accomplished through catalytic hydrogenation. The vegetable oil is first heated and mixed with a hydrogen gas stream, and then passed over a metal catalyst, such as nickel or palladium, that promotes the addition of hydrogen to the double bonds. The reaction is typically carried out at high pressure and temperature, and the degree of hydrogenation can be controlled by adjusting the reaction conditions.
However, the production of margarine has come under scrutiny in recent years due to the health risks associated with trans-fats. Trans-fats have been linked to an increased risk of heart disease and other health problems, and as a result, many countries have implemented regulations to limit or ban their use in food products.
As a result, many margarine manufacturers have shifted to using alternative methods of producing a solid spread, such as interesterification. Interesterification involves rearranging the fatty acids in the vegetable oils to produce a more solid consistency, without the need for hydrogenation or the formation of trans-fats.
In summary, the reduction of alkenes and alkynes is a critical process in the production of margarine and other food products. However, the health risks associated with trans-fats have led to the development of alternative methods of producing solid spreads that do not require hydrogenation.
White paper on Reduction of Alkenes and Alkynes
Introduction:
The reduction of alkenes and alkynes is a fundamental chemical process that has important industrial applications. Reduction can be achieved through various methods, such as catalytic hydrogenation, borane reduction, dissolving metal reduction, and sodium amalgam reduction. In this white paper, we will explore the different methods of reduction, their applications, and the challenges associated with their use.
Catalytic Hydrogenation:
Catalytic hydrogenation is a commonly used method for the reduction of alkenes and alkynes. It involves the addition of hydrogen gas to the double or triple bond of the alkene or alkyne in the presence of a metal catalyst, such as palladium or nickel. This method is widely used in the production of fuels and other chemicals from crude oil or natural gas.
The main challenge associated with catalytic hydrogenation is the formation of by-products, such as cis/trans isomers, and the potential for over-reduction. The degree of hydrogenation can be controlled by adjusting the reaction conditions, such as pressure and temperature, and the choice of catalyst.
Borane Reduction:
Borane reduction involves the addition of a borane, such as BH3, to the double or triple bond of the alkene or alkyne, which results in the formation of a borane-alkene or borane-alkyne complex. The borane-alkene or borane-alkyne complex is then reduced with a hydride source, such as sodium borohydride or lithium aluminum hydride, to produce the corresponding alkane or alkene.
This method is commonly used in the production of pharmaceuticals and specialty chemicals. The main challenge associated with borane reduction is the toxicity and volatility of borane, which requires specialized handling and equipment.
Dissolving Metal Reduction:
Dissolving metal reduction involves the use of an alkali metal, such as sodium or lithium, dissolved in liquid ammonia. The alkene or alkyne is added to the solution, and the metal reduces the double or triple bond to a single bond. This method is commonly used in the production of pharmaceuticals and agrochemicals.
The main challenge associated with dissolving metal reduction is the high reactivity of the alkali metal, which can result in explosive reactions if not handled properly. The use of liquid ammonia also requires specialized equipment and handling.
Sodium Amalgam Reduction:
Sodium amalgam reduction involves the use of sodium metal dissolved in a mercury solution. The alkene or alkyne is added to the solution, and the sodium amalgam reduces the double or triple bond to a single bond. This method is commonly used in the production of vinyl chloride, which is a key intermediate in the production of PVC.
The main challenge associated with sodium amalgam reduction is the toxicity of mercury, which requires specialized handling and disposal.
Conclusion:
In conclusion, the reduction of alkenes and alkynes is a fundamental chemical process that has important industrial applications. The choice of method depends on the specific reactants and desired products, as well as the desired reaction rate and selectivity. Each method has its advantages and limitations, and it is important to select the appropriate method for a given reaction. While the reduction of alkenes and alkynes is an important process, it is also associated with challenges, such as the formation of by-products, toxicity of reactants and reagents, and specialized handling and equipment requirements.