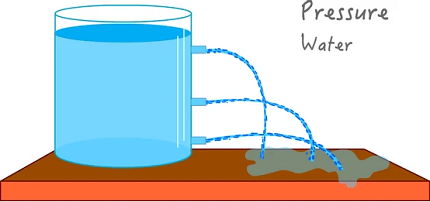
Pressure in a fluid is the force per unit area that the fluid exerts on the surface it comes in contact with. This pressure is a result of the motion and collisions of the individual particles of the fluid, such as molecules or atoms, and is described by the fluid’s properties, such as its density and temperature.
The pressure in a fluid is typically measured in units of pascals (Pa) or pounds per square inch (psi). The pressure at a point in a fluid can be calculated using the following formula:
P = ρgh + Patm
where P is the pressure at the point, ρ is the density of the fluid, g is the acceleration due to gravity, h is the vertical height of the point above a reference point, and Patm is the atmospheric pressure at the surface of the fluid.
This formula assumes that the fluid is at rest and is not flowing, and that the pressure is the same in all directions at a given point. In a flowing fluid, the pressure can vary depending on the speed and direction of the flow, and is described by the fluid’s flow equations, such as the Bernoulli’s equation.
What is Required Pressure in a fluid
The required pressure in a fluid depends on the specific application or situation in which it is used. For example, in a hydraulic system, the required pressure may be determined by the force needed to move a piston or cylinder. In a water supply system, the required pressure may be determined by the height of the building or the distance from the water source to the point of use.
In general, the required pressure in a fluid is the minimum pressure needed to achieve a desired outcome or perform a particular task. This pressure may need to be maintained at a constant level or it may need to vary depending on the conditions or demands of the system.
To determine the required pressure in a fluid system, various factors need to be considered, such as the type of fluid, the flow rate, the size and shape of the pipes or channels, and the forces acting on the system. This information is used to calculate the pressure drop or head loss in the system and to determine the necessary pressure to maintain the desired performance.
When is Required Pressure in a fluid
The required pressure in a fluid is necessary when the fluid is used in a system or process that requires a certain level of pressure to achieve the desired outcome. This can occur in a variety of applications and industries, such as:
- Hydraulic systems: In hydraulic systems, the required pressure is necessary to generate the force needed to move mechanical components, such as pistons, cylinders, and motors.
- Water supply systems: In water supply systems, the required pressure is necessary to ensure that water reaches all parts of the building or facility, and to provide adequate flow rate for various applications, such as drinking water, washing, and irrigation.
- Oil and gas industry: In the oil and gas industry, the required pressure is necessary to move the fluids through pipelines, wellbores, and drilling operations.
- Manufacturing processes: In manufacturing processes, the required pressure is necessary to control the flow of fluids, such as gases, liquids, and powders, in various stages of production, such as mixing, blending, and spraying.
- Environmental applications: In environmental applications, the required pressure is necessary to transport fluids, such as water, wastewater, and sludge, in treatment plants, pumping stations, and distribution networks.
In all of these applications, the required pressure is critical to the proper functioning of the system and to achieve the desired outcome.
Where is Required Pressure in a fluid
The required pressure in a fluid is typically found in a closed or open system, where the fluid is used to perform a specific function or task. The location of the required pressure depends on the specific application and the components of the system.
In a closed system, the required pressure is maintained within the system by a pressure regulator, which ensures that the pressure remains within a specified range. Examples of closed systems include hydraulic systems, pneumatic systems, and closed-loop circulation systems.
In an open system, such as a water supply system, the required pressure is typically measured at a specific point in the system, such as at a valve or faucet, and is maintained by adjusting the flow rate or by using a pressure regulator.
In some systems, such as in the oil and gas industry, the required pressure may be found at various points along the pipeline or wellbore, depending on the pressure needed to move the fluids through the system.
Overall, the location of the required pressure in a fluid depends on the specific application and the components of the system, and may vary depending on the desired outcome and performance requirements.
How is Required Pressure in a fluid
The required pressure in a fluid is determined by a combination of factors, such as the desired outcome, the characteristics of the fluid, and the components and conditions of the system. The pressure can be calculated or measured using various methods and devices.
One method for determining the required pressure is to use the Bernoulli’s equation, which relates the pressure, velocity, and height of a fluid in motion. This equation can be used to calculate the pressure drop or head loss in a system, which is the decrease in pressure due to the resistance of the fluid moving through pipes, valves, and other components.
Another method for determining the required pressure is to measure it directly using pressure sensors, such as gauges, transmitters, or transducers. These sensors can be placed at various points in the system to measure the pressure and provide feedback to a control system or operator.
In hydraulic systems, the required pressure can be adjusted by controlling the flow rate of the fluid using valves, pumps, or other components. In water supply systems, the required pressure can be adjusted by using pumps or pressure regulators to maintain the desired level of pressure.
Overall, the method for determining and maintaining the required pressure in a fluid depends on the specific application and the components of the system, and may involve a combination of calculation, measurement, and control techniques.
Structures of Pressure in a fluid
Pressure in a fluid exerts a force on the surrounding structures, which can have a significant impact on their stability, design, and performance. The structures of pressure in a fluid can be classified into two main categories: static pressure and dynamic pressure.
- Static Pressure: Static pressure is the pressure exerted by a fluid on a stationary object or surface. It is equal in all directions and is perpendicular to the surface. The static pressure in a fluid is determined by the weight of the fluid above the point of interest, and it increases with the depth of the fluid.
The structures that are affected by static pressure in a fluid include dams, retaining walls, and water tanks. These structures need to be designed to withstand the pressure exerted by the fluid, which can be calculated based on the density and depth of the fluid, as well as the geometry and materials of the structure.
- Dynamic Pressure: Dynamic pressure is the pressure exerted by a fluid on a moving object or surface. It is caused by the kinetic energy of the fluid in motion and is proportional to the velocity of the fluid.
The structures that are affected by dynamic pressure in a fluid include bridges, offshore platforms, and aircraft wings. These structures need to be designed to withstand the pressure and forces exerted by the fluid, which can be calculated based on the velocity and density of the fluid, as well as the geometry and materials of the structure.
In addition to static and dynamic pressure, other structures of pressure in a fluid include hydrostatic pressure, which is the pressure exerted by a fluid due to its weight, and hydrodynamic pressure, which is the pressure exerted by a fluid in motion due to its viscosity and turbulence.
Case Study on Pressure in a fluid
One example of the importance of pressure in a fluid can be seen in the design and operation of hydraulic systems. Hydraulic systems use fluids, typically oil or water, to generate force and motion in mechanical components, such as cylinders, motors, and valves.
In hydraulic systems, pressure is a critical parameter that affects the performance, efficiency, and safety of the system. The required pressure depends on the specific application and the components of the system, and it can range from a few hundred to thousands of pounds per square inch (psi).
A case study that illustrates the role of pressure in a hydraulic system is the design and construction of an excavator. An excavator is a heavy construction machine that is used to dig, move, and lift soil, rocks, and debris. The excavator consists of several hydraulic components, such as pumps, motors, cylinders, and valves, that work together to generate the force and motion needed for digging and lifting.
The pressure in a hydraulic excavator is critical to its performance and efficiency. The required pressure depends on several factors, such as the weight and size of the excavator, the type of soil or material being excavated, and the depth and angle of the excavation.
To ensure that the excavator meets the required pressure and performance specifications, the hydraulic system is designed and tested using computer simulations and physical prototypes. The pressure is monitored and controlled using sensors and feedback systems that adjust the flow rate and pressure of the fluid.
In addition to performance and efficiency, pressure in a hydraulic excavator also affects its safety. Excessive pressure can cause damage to the components of the system, leading to leaks, failures, and accidents. Therefore, pressure relief valves and other safety devices are used to prevent over-pressurization and ensure the safe operation of the excavator.
Overall, the case study of an excavator illustrates the importance of pressure in a hydraulic system and the role of design, testing, and safety measures in achieving the desired outcome. The proper management of pressure in a fluid is crucial to the performance, efficiency, and safety of many engineering systems and applications.
White paper on Pressure in a fluid
Introduction:
Pressure in a fluid is a fundamental concept in fluid mechanics and engineering. It refers to the force exerted by a fluid per unit area, and it plays a critical role in the behavior, performance, and safety of fluid-based systems and applications.
This white paper provides an overview of pressure in a fluid, including its definition, units, sources, and effects. It also discusses the different types of pressure and their applications, as well as the methods for measuring, calculating, and controlling pressure in a fluid.
Definition and Units of Pressure:
Pressure in a fluid is defined as the force per unit area exerted by the fluid on a surface or object. It is expressed in units of pressure, such as pounds per square inch (psi), pascals (Pa), or bars (bar).
The pressure in a fluid can be calculated using the following formula:
P = F/A
Where P is the pressure, F is the force exerted by the fluid, and A is the area of the surface on which the force is applied.
Sources and Effects of Pressure:
Pressure in a fluid can arise from various sources, such as gravity, motion, temperature, and external forces. For example, the pressure in a fluid due to gravity is known as hydrostatic pressure, and it increases with the depth of the fluid. The pressure in a fluid due to motion is known as dynamic pressure, and it increases with the velocity of the fluid.
The effects of pressure in a fluid depend on the application and the components of the system. In some cases, pressure can cause deformation, buckling, or failure of structures, while in other cases, it can generate force and motion for mechanical components. Pressure can also affect the efficiency, performance, and safety of fluid-based systems, such as pumps, turbines, and hydraulic systems.
Types of Pressure and Applications:
There are several types of pressure in a fluid, including static pressure, dynamic pressure, hydrostatic pressure, and hydrodynamic pressure.
Static pressure is the pressure exerted by a fluid on a stationary object or surface. It is equal in all directions and is perpendicular to the surface. Static pressure is important in the design and analysis of structures, such as dams, tanks, and pipelines.
Dynamic pressure is the pressure exerted by a fluid on a moving object or surface. It is caused by the kinetic energy of the fluid in motion and is proportional to the velocity of the fluid. Dynamic pressure is important in the design and analysis of structures, such as aircraft wings, wind turbines, and offshore platforms.
Hydrostatic pressure is the pressure exerted by a fluid due to its weight. It increases with the depth of the fluid and is important in the design and analysis of structures, such as dams, water tanks, and underwater vehicles.
Hydrodynamic pressure is the pressure exerted by a fluid in motion due to its viscosity and turbulence. It is important in the design and analysis of fluid-based systems, such as pumps, turbines, and hydraulic systems.
Measuring, Calculating, and Controlling Pressure:
Pressure in a fluid can be measured using various methods, such as pressure gauges, transmitters, and sensors. These devices can provide accurate and real-time measurements of pressure, which can be used to monitor and control fluid-based systems.
Pressure in a fluid can also be calculated using mathematical models and equations, such as Bernoulli’s equation and the Navier-Stokes equations. These models can provide insights into the behavior and performance of fluid-based systems, such as the flow rate, pressure drop, and turbulence.
Pressure in a fluid can be controlled using various techniques, such as valves, pumps, and regulators. These devices can adjust the flow rate and pressure of the fluid, which can be used to optimize the performance, efficiency, and safety of fluid-based systems.